The Right Team + The Right Technologies
We're able to make repeatable parts to precise tolerances by using top of the line equipment. From our 5x10 fiber laser, 7 axis CNC press brake, and fastidious design, the tools and passionate team we employ guarantees an exceptional product.
Our campers are manufactured with tried and true methods; our customers are not a large, expensive experiment. We're extremely proud of what we build, and we'll continue to put quality over profit and customer satisfaction over our bottom line.
Bends & Welds
We construct our campers with laser cut and formed 5052 aluminum sheet, laser cut and welded 6061 structural aluminum tube. There is an inherent sheer strength to our campers making them extremely robust, as with each bend the metal becomes stronger. There is no question about it. Bending and welding beats out bolting and riveting. Just ask an engineer.
Canvas & Finish
Our tents are sewn in-house with premium fabric Top Gun 9 (Made in USA). An acrylic coated polyester that can stand up to the rigors of life in the elements. -40º F crack test pass, 50,000 abrasion cycle pass; it's the right material for the job.
Our powder coating process uses the gold standard of exterior grade powder coat (Tiger Drylac SUPER DURABLE series powders). Double action sanded and solution cleaned before application, with excellent results to date. And we should know, we live on the beach.
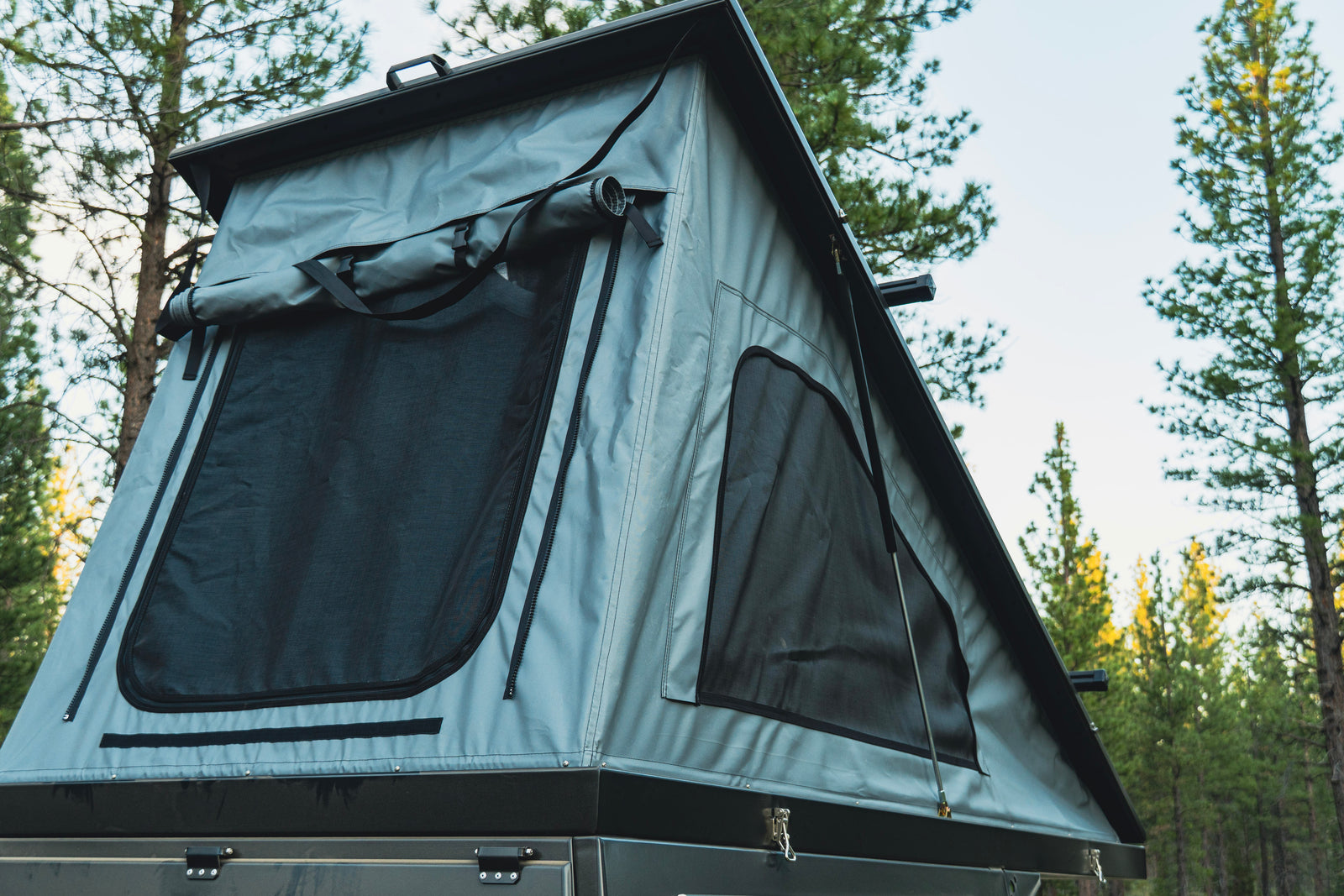
Aluminum Vs. Composite
Composites fail where aluminum won’t. Why do we use single sheet aluminum for our roofs? A look at other companies will give your answer. Plastic honeycomb composite called plascore will degrade from UV exposure, and has the risk of delamination. Aluminum composite panels (ACM) are originally designed for sign boards, not off road campers.
Your camper should last decades, not seasons.
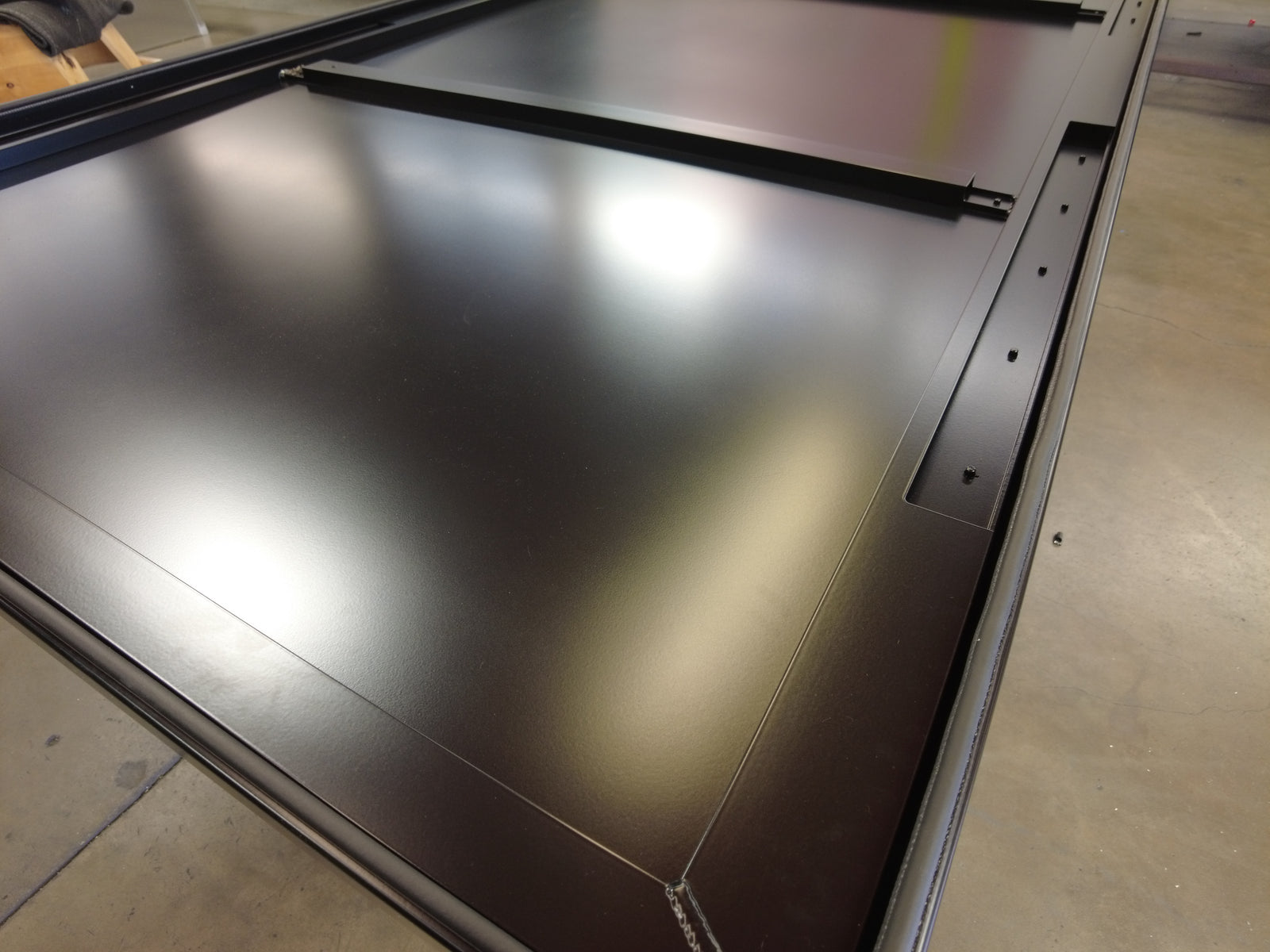
To Extrude or Not to Extrude
Why do most companies choose to use bolted extrusion frames? The simple answer is it doesn’t require a skilled workforce to assemble. So in short, it's cheap and easy.
Downsides of extrusions are:
- 6000 series extruded aluminum is brittle when tapped and bolted with stainless hardware. Not to mention the potential for dielectric corrosion from dissimilar metals as many using threaded stainless hardware.
- Most extrusions are anodized, not powder coated. Anodizing is a poor choice for exterior applications and will fade quickly.